Injection Mollding Process: IML (In-Mold Labeling)
In-mold labeling (IML) was first used in the mid-1970s as an alternative to decals and pressure-sensitive labels. IML’s Chinese name: In-Mold Labeling process Its very distinctive features are: the surface is a hardened transparent film, the middle is the printing pattern layer, and the back is the plastic layer.
As the ink is sandwiched in the middle, it can effectively prevent the product ink layer from scratching, and can keep the color vivid and not easy to fade for a long time.
Mold Labeling IML is a new type of in-mold decoration technology that combines screen printing, molding, and injection molding, in terms of product decoration.
In-mold decorating (IML) is one of the most effective and cost-saving methods, and its diverse applications have made in-mold decoration an ideal replacement for many traditional processes: such as thermal transfer, direct surface printing, surface coating, direct plating, two-color injection molding, and other traditional decoration methods.
It is most suitable for 3D products, especially where consistent overlay patterns, backlighting, and multiple colors are required and should be reflected on various curved, curved, and beveled surfaces.
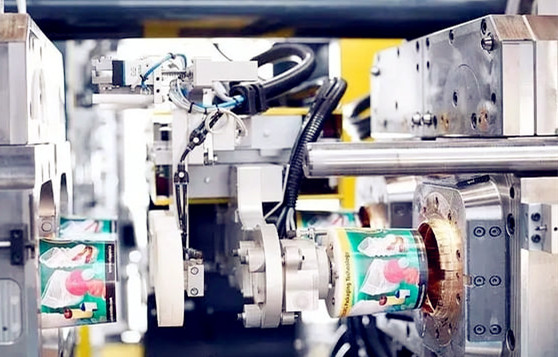
Concept of IML
IMD (In-Mold Decoration) is a technique to decorate the surface of molded plastic appearance by placing Film inside the injection mold.
Currently, there are two manufacturing methods of IMD, one is to make the printed Film film into a circular roller rolled tape, installed inside the injection mold, like a label Label attached to the mold surface fully automated circular belt moving type production; ink layer and film separation bonded to the surface of plastic products, that is, people call IMD (in-mold thermal transfer printing).
The other is to print the film through the forming injection molding machine forming and then after cutting placItsed it into the injection mold production out. That is called IML (in-mold labeling), this Film can generally be divided into three layers: substrate (generally PET, PC, PMMA), ink layer (INK), and an adhesive material (mostly a special adhesive).
When the injection molding process is completed, through the role of adhesive glue to make Film and plastic closely combined into one, because the product itself is covered with the wear-resistant substrate in the outermost layer, wear-resistant, and scratch-resistant role, its surface hardness can reach 3H, where the injection material is mostly PC, PMMA, ABS, PC/ABS and so on.

The process of IML
Cutting material — plane pad printing — ink drying fixed — paste protective film — punching positioning holes — thermoforming — shear peripheral shape — label material injection molding. Specific instructions are as follows.
1. Cutting material
Cut the rolled film Film into square blocks of designed size for the printing and forming process.
2. Flat printing
According to the requirements of the icon, text into a film screen, in the cut film Film square block printing icon, text.
3. Ink drying
The printed film is placed in a high-temperature oven to dry.
4. Protective film
To avoid blurring the surface of the printed film when punching the positioning holes, sometimes a single or double layer of protective film needs to be applied (required for products with windows).
5. Punching positioning holes
Punching the positioning holes on the printed film to ensure the accuracy of the hot pressing position.
6. Thermoforming (high pressure or copper mold)
After heating the printed film, use a high-pressure machine or copper mold to form it in preheated condition.
7. Shear peripheral shape
Cut off a scrap of the formed three-dimensional film.
8. Material injection
Put the film which is the same as the three-dimensional shape of the front mold after molding onto the front mold and inject the finished IML product.
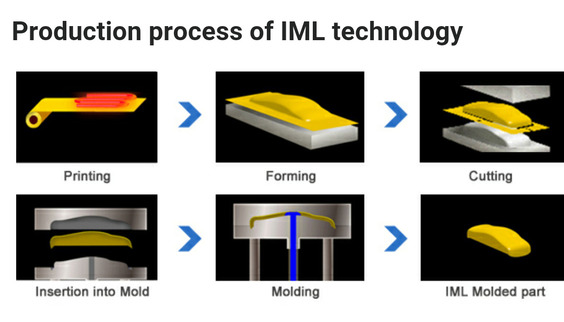
Features of the IML process
1. The whole manufacturing entire process, from the printing and forming of the sheet, the design and production of the mold to the re-molding of the injection, is done in-house; it greatly reduces the development time and ensures on-time delivery.
2. Flexibility in design gn, rapid product diversification at a lower cost.
3. No need for panel paste, no adhesive of any capacitor type, in line with environmental requirements.
4. keys can be protruded during in-mold injection, and the life of keys can be played 1 million times; realize high-precision decoration of three-dimensional surface, and the decorative patterns are hidden inside and never wear out (unless destroyed)
5. Higher scratch resistance and light transmission, easy to achieve permanent clear display.
6. 3D blow molding, strong three-dimensional sense, so that complex component can also achieve a high level of decoration.
7. Give end-users more beauty, lighter, more thin solid layers, more options, and more safety.

Advantages and disadvantages of the IML process
Advantages
1. Product stability: the product produces consistency and standardization of the correct set of colors
2. Product durability: Through the protection of special treatment of COATING film, it can provide excellent surface wear resistance, corrosion resistance, dustproof, moist
3. 3D complex shape design: the application of film with excellent stretchability, can smoothly achieve the required product complexity of external design needs
4. Diversified styles: color can be changed at will, multiple colors can be expressed, patterns can be changed at will, and special patterns with metallic, plating or natural materials can be created according to customer needs.
5. IML production batch quantity is flexible and suitable for multi-variety small quantity production.
Disadvantages
1. Long pre-production plastic injection molding cycle and many processes.
2. Easy to produce film peeling, distortion, deformation, etc.
3. High defective rate of products.
.
IML design considerations
1) Injection thickness: It is recommended that the average flesh thickness should not be less than 1.2 mm (1.0 mm without Film).
2) Film thickness specifications are: 0.1 mm, 0.125 mm, 0.175 mm, 0.2 mm.
3) Film single printing, more suitable for a small number of diverse design occasions.
4) The appearance of the color is bright silver, electroplated silver, and other metallic colors do not apply to this practice, easy to cause the film due to high and low-temperature peeling.
5) The size of the outer edge of the film is related to the size of the mold cavity, too small or too large will cause the mold cavity to stretch the edge of the white or crimped edge.
6) The minimum diameter of the round hole on the Lens is Φ1.0 mm.
7) Lens P.L position is generally at the bottom of the Lens if the problem of mold pulling angle can be at the position of 0.2 mm under the edge of the Film cover.
8) The extraction angle of the Lens is generally at least 3º.
9) For the case of difference in the appearance of Lens, the film must be molded plastic part beforehand.
10) Design of rounded corners: The appearance of IML injection molding cannot cause a sharp appearance, and the appearance profile should avoid sharp corners, so there should be no sharp corners in the design, and the corners of the product must be rounded (at least 0.3R).
11) Wrap edge problem: The wrapped edge refers to the part of the edge where the laminate is joined with the plastic. This edge is not possible to do very neatly after injection molding, therefore, when we design the application of IML products, the edge can be blocked with plastic parts.

Comparison of the characteristics of IML and IMD
1) IMD is suitable for large batch quantities (100,000) and above. IML is flexible in producing batch quantities.
2) IMD pattern three-dimensional molding height not more than 1.5MM IMD products.
IML can process a variety of complex three-dimensional production, such as flat, curved, wrapped edges and other kinds of products, 3D pattern three-dimensional forming up to 40MM.
3) IMD products, because the ink screen printing on the surface, so the font is easy to fall off.
IML ink screen printing in the middle layer, the appearance of clean and beautiful, with excellent scratch chemical resistance, and in the production can change the pattern and color at any time.
4) IMD printing technology is very demanding, only a few large manufacturers control it, and mass production is limited by the manufacturer’s film supply.
IML printing technology is relatively low, and the screen printing color can be changed at any time in the production of the same batch.
IML sheet material is divided into PET, PC, and PMMA, material can be divided into A, transparent: sanding surface, brushed and other patterns, etc. B, plating C, artificial leather, hair.
5) IMD cannot do with keys.
IML can do products with keys
6) IML can be developed in a short period (while developing the open plastic injection mold, it can develop the mold for molding and punching, and other auxiliary processes can be completed at the same time);
Several parts can be produced together, so the cost is relatively reduced; because there is no hook, so the thickness of the product can be produced relatively thin.
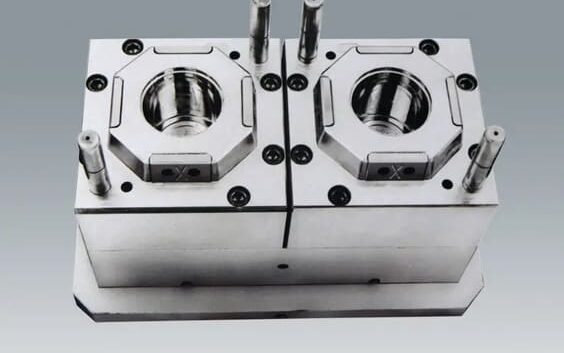
IML application fields
IML products with high clarity, good three-dimensional sense, and the scratch-resistant surface can change the design pattern at will, enhance the product’s beautiful appearance, reflect the advantages of the perfect shaped structure, to solve the previous acrylic plate can not achieve the shaped effect and a variety of colors.
Widely used in communication products (such as cell phone / small mobile phone lens, decorative parts, shell, etc.), IT products (notebook computers, etc.), household appliances (window panels, key panels, decorative panels, etc.), medical equipment (window lenses, housings, decorative parts, etc.), automotive dashboards and anti-counterfeit markings.